With the rise in popularity of electric vehicles, manufacturers are racing to increase EV production without compromising quality. Statistics show that by the end of 2025, 85 million electric vehicles are expected to be on the road globally. This increase in EVs affects EV battery production as it is the heart of any electric vehicle.
Table of Contents
ToggleWhat Are Electric Car Batteries Made Of?
Want a quick, visual breakdown of how electric car batteries are made? Watch this 2-minute video to see the entire EV battery manufacturing process. For a more detailed explanation, continue reading below! 👇
Electric car batteries are made of various components including rare earth metals such as Lithium, Nickel, Cobalt, Manganese etc… which need to be carefully handled and integrated. In simpler terms, EV batteries store chemical energy and convert it into electricity, which then powers the motor to move the vehicle.
Key Components of Electric Vehicle Batteries
Electric car batteries are made up of several cells, these cells can be in various shapes such as Cylindrical, Prismatic or Pouch depending on the make, model, power and range of the electric vehicle.
Before understanding the EV battery manufacturing process, it is important to learn the battery composition, as it will give you a better grasp of how EVs work.
The key components of the EV battery are:
- Anode– This is the negative electrode and is typically made of graphite and small quantities of lithium.
- Cathode– This acts as the positive electrode and is composed of Manganese, Nickel, Cobalt and lithium.
- Separator– A micro permeable membrane separator is required to prevent any physical contact between the anode and cathode and to ensure proper ionic reactions between the anode and cathode.
- Electrolyte– The solution which helps in the conduction of electricity via ions, majorly this is a lithium-based solution known as lithium hexafluorophosphate.
- Cell Casings– Typically made of nickel-plated steels to avoid electrolytic reactions, is the enclosure for the cell.
How EV Batteries Are Made: Step-by-Step Process
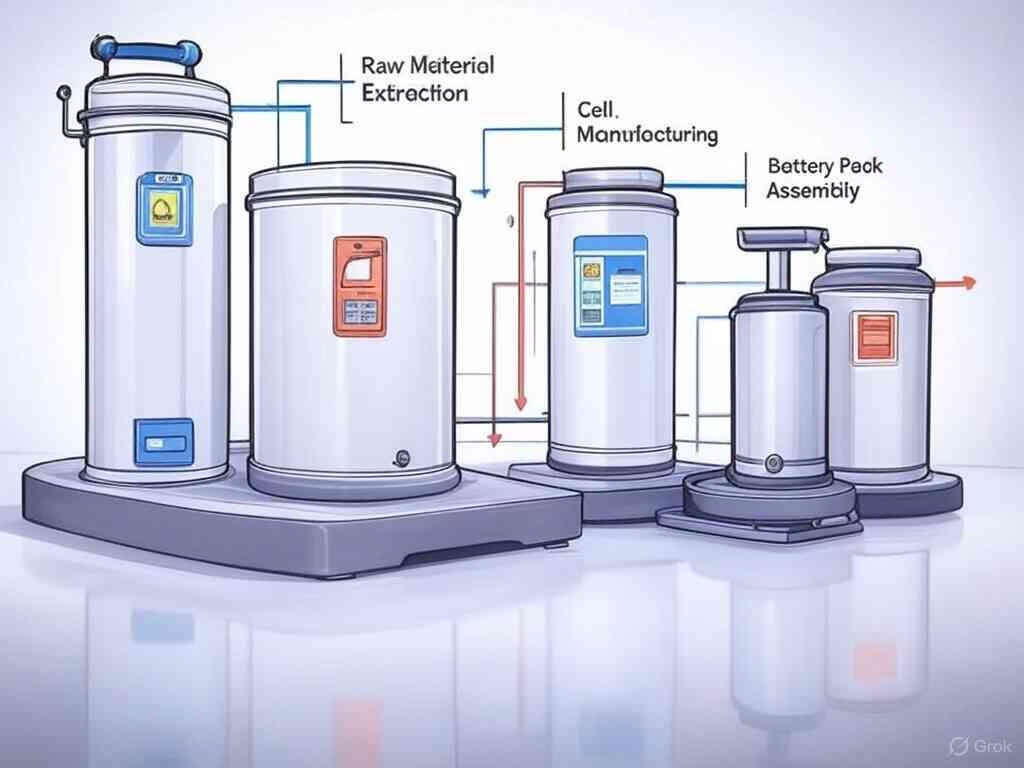
Electric vehicle batteries build on the same lithium-ion technology as smartphone batteries but are engineered for greater energy capacity and range. Now, let’s understand how these batteries are made, this is a long process that involves Extraction, Processing and Construction.
- Extraction– Materials like lithium, nickel and cobalt are mined using various methods depending on the geographical location of the resources. Typically, these are found across the globe but mainly concentrated in Africa, Latin America and Australia.
- Processing– The extracted materials are then processed in plants and refineries, converting them to anodes and cathodes. These act as positive and negative charges of the cell facilitating the chemical reaction
- Construction– The batteries are composed of modules, the modules consisting of cells, after processing are sent for construction, where the battery pack is assembled by packing multiple cells together. This is a highly critical stage, as it is the ultimate quality control point, any leaks or defects in the cells could damage the battery, and hence this field is integrating automation and robotic technology to avoid human error.
The finished battery packs are then sent to the electric vehicle manufacturer, who in turn install them in their cars. The size of the battery depends on the type of the vehicle and power required for the drive.
Challenges in EV Battery Manufacturing
EV battery manufacturing comes with its fair share of complications, which need to be solved as the future demands a rise in production. Lets look at the key challenges that are to be tackled:
- Safe processing practices– electric car batteries are made up of cells, which need to be maintained in an optimum temperature range, any drastic fluctuations could cause fire. To help the integrity of the battery packs, sometimes lateral braces are used, and the spot welding done for the same can cause splatter or overheating which will affect the sensitive cells.
- Operator safety– These are highly flammable and toxic materials, which could combust and start fires if not handled properly. Hence ensuring operator safety is one of the main challenges of the EV battery manufacturing process.
- Ethical sourcing– The Democratic Republic of Congo is one of the leading suppliers of cobalt required for EV batteries. However, studies show that there are unethical practices including child labor and subhuman working conditions. Mining natural resources also poses other threats such as pollution and contamination of groundwater sources.
- Quality checks– Quality is of utmost importance in this industry, as the integral component for an electric vehicle, any faulty battery could lead to dangerous situations and expensive recall procedures. Hence the quality check is a long and exhausting procedure which requires a lot of manpower.
- Cost– With all the extra precautions and standards, EV battery manufacturing is a costly affair. With the increase in the market players are calling for cheaper versions of the vehicle without compromising the quality. This is pushing the developers to innovate and optimize the current facilities to reduce the number of rejections and wastage.
Although the challenges are daunting, it is not impossible to find solutions for this. With the advancements in technology and automotive giants investing billions in alternative solutions, these challenges will soon be a thing of the past.
Future Trends in EV Battery Manufacturing
With around a 30% increase from the current market share, Electric vehicles are set for record-breaking sales by 2030. And this calls for newer trends that will shape the industry
- Range– Companies are looking towards increasing the range while reducing the battery size, lightweight batteries are currently under development.
- Charging capacity– With the upcoming modifications, EV manufacturers are aiming at increasing the charging capacity while reducing the damage to the battery caused by DC fast charging.
- Solid state batteries– The environmental concern regarding the sourcing of the natural resources required for the Lithium-ion battery is creating waves in the industry, and solid-state batteries are one futuristic collusion which is under development.
Must read on Solid State Battery vs Lithium-Ion to learn the difference.
Conclusion
The EV battery manufacturing process is one of the most quality-driven processes out there due to the nature of the application. The batteries are made with longevity and durability in mind and hence held to the highest standard. The used batteries can be recycled, and the minerals are extracted to be utilized in various other industries as a part of the sustainability movement.
With the surge in demand, the facilities and manufacturers are adopting sustainable practices with long-term guarantees ensuring a golden future for the EV industry.
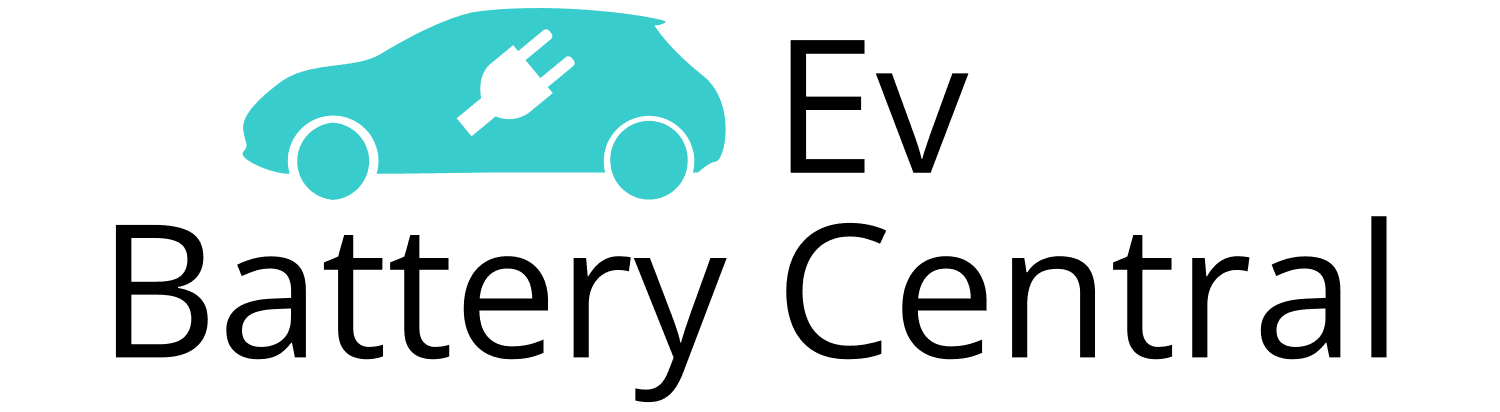
EV Battery Central is your trusted source for EV battery insights. We provide expert guidance on battery maintenance, recycling, replacement costs, and innovations in electric vehicle technology. Our mission is to empower EV owners with actionable information to make informed decisions.